Before we start working on a new project for a customer, we always want to get project specifications first. We have over 40 years of experience in all kinds of blow-molded bottles and containers and building a tool for manufacturing. It is important to work with an experienced molder that you are comfortable with. We have dozens of stock bottles and containers, but if you need something more unique, we can work with you on a custom tool.
At Apex Plastics, our staff will walk you through the steps necessary to have a new tool built for your blow molding project.
What is the anticipated volume for your project?
The anticipated volume to be produced with each run or annually will determine how many cavities your tool will need. Number of cavities or cavitation is how many parts will be made each time the machine cycles. Low volume parts may require only a single cavity, while higher volume parts may necessitate a higher number of cavities. Apex Plastics can produce low volume parts in 1 or 2 cavity molds or higher volume parts on 4, 6, or 8 cavity molds. While adding additional cavities will increase the initial investment, in the long term it can decrease the price per part and position your product for growth.
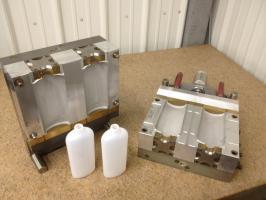
Determining the Best Tool Maker
Apex Plastics partners with a variety of tool builders with a wide variety of expertise when building a tool for manufacturing. Richard Bell, our Tool Manager, a 25-year veteran of the blow molding industry, offers the following advice, “Different tool makers have different specialties, so consulting with your molder is a good way to make sure that your needs are going to be met.“
Our experienced staff will consult with you on types of materials and their impact on the tool’s price. Things to consider when determining material for mold is the initial investment, the tool’s life, maintenance costs, along with annual output volumes.
A mold built with lower quality materials may be less expensive initially, but may require more maintenance or need costly repairs over the life of the tool. Whereas a higher quality material mold may reduce overall maintenance costs, but has a higher initial investment.
We understand that the decision to build a new blow molding tool is significant to your business. Consulting the right experts is important to making the experience satisfying and productive. Our sister company, HTI Plastics builds tools as well.
When considering a project that requires a new blow molding tool consider Apex Plastics. Our deep industry relationships and over 40 years of experience allow us to help you make the right decision on your next blow molding project.