The blow molding process is the manufacturing process by which hollow plastic parts like bottles and containers are formed. At Apex, we use a process called continuous extrusion blow molding to turn raw plastic into high-quality finished products for our customers.
Preparation
Naturally, the blow molding process begins when we bring raw plastic to the machine, but there are preparatory steps for each product we make. Plastic can either be processed in its natural state or it can be blended with a wide variety of colors and additives.
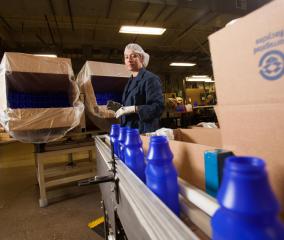
Extrusion
A screw inside the barrel on the extruder turns continuously, pushing the plastic down the length of the barrel. Through mechanical friction, the plastic is transformed from solid pellet form into a molten state that allows it to be formed into shapes. Heaters on the barrel and head maintain a uniform temperature, creating material consistency, as the plastic moves through the barrel. The evenly heated molten plastic is then pushed through an extrusion head and past die tooling that forms a parison.
Forming a Parison
The parison is a hollow tube of plastic that will become the final bottle, container, or shape. The extrusion head and die tooling determine the shape and quantity of parisons that will be produced. For heavy or large parts, a single extrusion head may be used, allowing only one part to be made during each cycle of the machine. Smaller parts made on the same machine may use extrusion heads capable of making multiple parisons. This allows multiple parts to be made during each machine cycle.
Mold it!
The extruded parison is then clamped into a mold and cut. Next, a blow pin enters the top of the parison to seal the tube and compressed air pushes the plastic out to match the mold. Molds are commonly made of aluminum or other metals that can be cooled to facilitate the quick formation of the finished part. Once the plastic has cooled and hardened, the mold opens and the part is ejected. One piece down, many more to go!
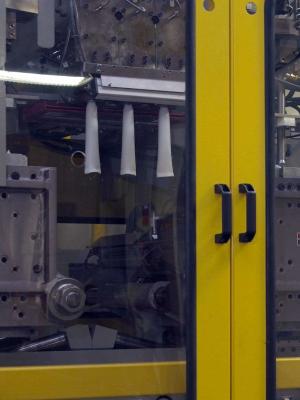
Recycling Plastic
Excess plastic, or flash, is removed from the mold either manually or by machine. The flash is sent through a grinder where it’s cut into small pieces and then transferred to a surge bin. The recycled material, or regrind, can be reintroduced to the manufacturing process through the material handling system keeping waste to near zero.
Learn more about the Apex Plastics company.
Check out our sister company, HTI Plastics.