With extrusion blow molding production, a good mold can get you a long way toward where you want to be. To get the rest of the way, the process – the type of plastic, processing parameters, head tooling selection, to name several – has to be carefully considered and controlled.
The process at Apex Plastics does not begin in earnest until a work order is generated from our Enterprise Resource Planning (ERP) system. The work order contains all of the information specific to the plastic bottle or container that has been agreed upon by Apex and the customer. The work order contains information such as container type, material to be used, color (if any), neck finish, as well as any special requirements. Once generated, the work order is distributed to the various teams creating the finished parts.
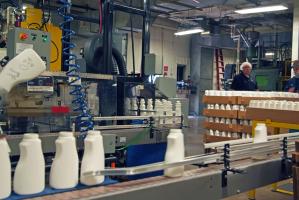
Once the work order is in hand, the set-up team begins work. The set-up team works closely with the quality and production teams to get plastic bottles, containers, or shapes into specification and ready to run in a production setting. They install the molds and head tooling on the blow molding machines that will ultimately create the final plastic parts. To ensure consistency, all process parameters are recorded at the beginning and end of each production run. These set-up and shut-down sheets are then consulted during ensuing production runs to help determine optimum processing parameters.
The set-up team relies on assistance from the production team in getting material to the machines that are being prepared for production. The work order designates the type of plastic the bottle, container, or shape will be made from and the color used if any. Material requiring color is mixed in precision gravimetric blenders and then moved to the machine through our advanced material handling system. The production team will then administer and monitor material throughout the production run.
Quality Assurance provides set-up and production with the required specifications to which the bottles will be manufactured. For the set-up team, the specifications are a target they must reach before the plastic bottle, container, or shape is turned over to production to run. For the production team, these specifications are what they will produce to throughout the course of production. They may also include special testing requirements and/or packaging instructions. As an ISO 9001:2015 registered facility, our Quality Management System (QMS) requires the entire process to be documented throughout.
Behind the scenes ,our maintenance department provides every one of our teams with a solid foundation to work from. They make sure that all of the equipment and systems are maintained and take care of occasional mechanical issues. Our extensive preventive maintenance programs allow Apex to run smoothly and efficiently. Preventive maintenance of plant systems such as air, water, and cooling, ensure that the process stays consistent.
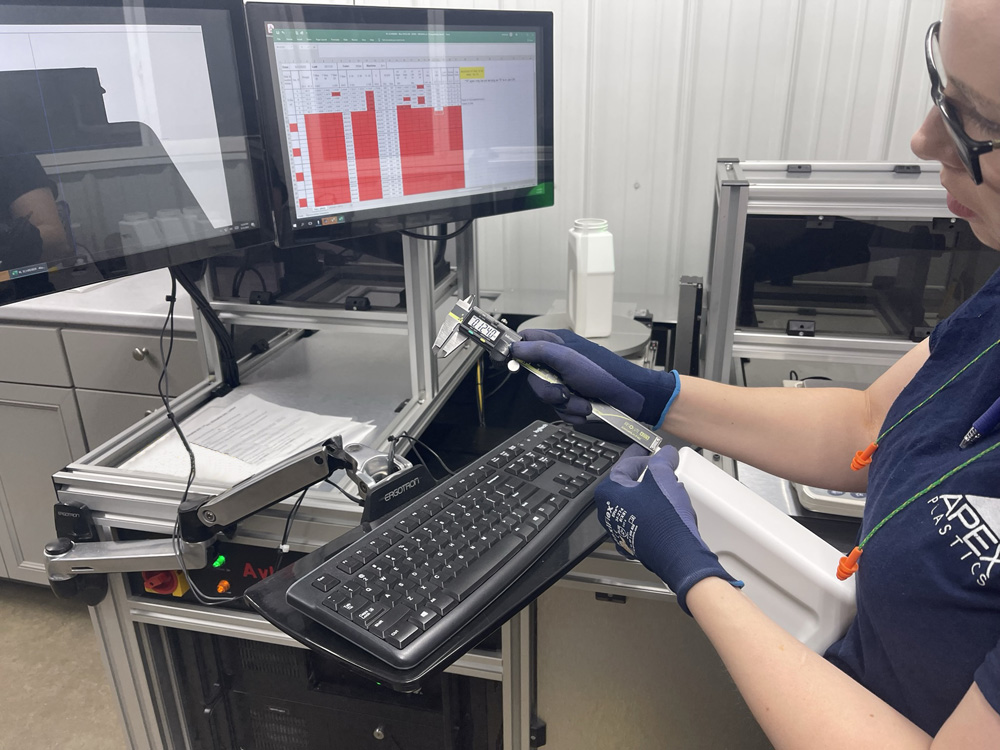
Making a plastic bottle, container, or shape requires a concerted effort from wide variety of specialties. By following documented and repeatable steps during the course of each production run, Apex is able to provide customers with quality containers when they need them.