During the extrusion blow molding process a parison is extruded, the bottom and top are pinched off, and then blown into the shape of the cavity. The excess plastic that is pinched off at the top and bottom of the mold cavity is known as flash. Removal of flash is done post-molding and requires removal either manually or mechanically. Any post-molding operations run the risk of damaging parts so minimizing and managing flash is important for quality parts.
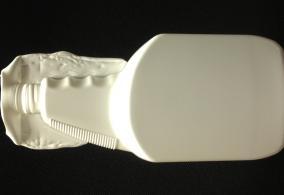
When designing a plastic bottle or container for extrusion blow molding, it is important to consider the impact of flash on the part. The shape and size of a bottle will determine the amount of flash that will be formed. For example bottles with an off-set neck, such as trigger sprayers, will require much more flash than bottles with a centered neck.
Flash can have an impact on both appearance and functionality of the plastic bottle or container. Plastic parts with excessive or ragged flash are not as visually appealing as parts with flash neatly removed. Too much flash at the neck of a plastic bottle can prevent closures from fitting properly.
The regular maintenance of extrusion blow molds that require large areas of flash is especially important. By keeping a properly raised pinch-off, the flash can be neatly and easily removed. Molds with worn or improperly maintained pinch-off can result in parts that are unacceptable. Both the mold and last run parts should be inspected regularly to make sure that the pinch is adequate and that all flash is being removed.
For more information on flashing and how we are tackling the issue at Apex, our recent newsletter on the topic goes into more detail. To find out how we can help you with your next custom blow molding project call us at 800-467-4640.
Visit our sister company, HTI Plastics.